


DTF PROCESS
What is DTF Printing?
The DTF process is as simple in its working as its name suggests – Print on a film and directly transfer it onto fabric. The most prominent factor that makes this process worthy of use across a larger number of people is the freedom to choose almost any fabric. Be it polyester, cotton, silk, or synthetic fibers like rayon or terry cot, the DTF printing process will work its magic on them.
The requirements for DTF printing do not demand a heavy investment from the user. Be it, someone who is currently engaged in one of the digital textile printing processes mentioned above and wants to shift to DTF printing as an extension of the business, or someone wanting to venture into digital textile printing starting with DTF, one has to invest in the following.
PRE-REQUISITES OR DTF PRINTING
01
Direct to Film Printer
These printers are often called DTF Modified Printers. The Apache DTF Printer work with 6 colors. This provides the convenience of operation as the CMYK DTF inks can go into the standard CMYK ink packs are easy to fill with ink, and even a small amount of ink can be transferred and used, so there is no wasted ink.
DTF Films
02
PET films are used in the DTF printing process. These films are different than those used in screen printing. These have a thickness of around 0.75mm and better transfer characteristics. In the language of the market, these are often referred to as DTF Transfer Films. DTF films are available in the form of A3 size
RIP Software
03
The software is an important part of the process. The print characteristics, color performance of the inks, and the final print performance on the fabric after transfer are greatly influenced by the Software. For DTF, one would require specialized RIP software that can handle CMYK and White Colors. The color profiling, ink levels, drop sizes and other factors contributing to an optimized print result are all governed by the DTF Printing software. Our Software used by Apache is very convenient and high functions because it contains various functions that users want.
04
Hot-melt adhesive Powder
The DTF printing powder is white and acts as an adhesive material that binds the colored pigments in the print to the fibers in the fabric. There are different grades of the DTF hot melt powder that are specified in microns. An appropriate grade should be selected based on requirements.
05
DTF Printing Inks
These are specially designed pigment inks available in Cyan, Magenta, Yellow, Black and White colors. The White Ink is a special component that lays out the white foundation of the print on the film and onto which the colored design is printed.
06
Curing Oven
The curing oven can also be used as a basic home oven or small industrial oven used to melt hot melt powder.
Transfer
07
This is the heart of the DTF printing process. The PET film with the image and the melted powder are placed on the pre-pressed fabric in the heat press for a strong adhesion between the film and the fabric. This process is also called ‘curing’. The curing is done at a temperature range of 140 to 150 degrees Celsius for approximately 10 to 20 seconds. The film is now firmly attached to the fabric.
08
Cold Peel
The fabric and the now attached film on it must cool down to room temperature before one pulls the film off. Since the hot melt has a nature similar to amides, as it cools down, it acts as a binder that holds the colored pigment in the inks in firm adhesion with the fibers of the fabric. Once the film is cooled, it must be peeled off the fabric, leaving the required design printed in ink over the fabric.
09
Post-pressing
This is an optional step but is very highly recommended for best results and high-performance parameters like wash and rub fastness. In this step, the final fabric with the transferred design is pressed in the heat press for around 10 to 15 seconds again.
DTF PROCESSING GUIDE
Print on Film
STEP 01
Instead of regular paper, insert the PET film into the printer trays. First, print the entire image in white on the PET film. After this, using the appropriate color settings in the printer, print the required image on the white image layer. The important point to remember is that the print on the film must be a mirror image of the actual image that needs to appear on the fabric.
STEP 02
Powdering
This step is the application of hot-melt powder on the film that has the printed image on it. The powder is applied uniformly when the ink is wet and the excess powder needs to be removed carefully. The important thing is to ensure that the powder is evenly spread all over the printed surface on the film.
One very common way to ensure this is to hold the film at its short edges such that its long edges are parallel to the floor (landscape orientation) and pour the powder in the middle of the film from top to bottom such that it forms an approximately 1-inch thick heap in the center from the top to the bottom.
Pick up the film together with the powder and slightly bend it inwards such that it forms a slight U with the concave surface facing oneself. Now rock this film from left to right very lightly such that the powder will slowly and evenly spread all across the surface of the film. Alternately, one can use automated shakers available for commercial setups
Melting the powder
STEP 03
As in the name, the powder is melted in this step. This can be done in various ways. The most common way is to put the film with the printed image and the applied powder in the Curing Oven and heat. If the curing oven is unavailable, place the film inside the heat press and bring the top of the press very close to the film but not touching it.
There should be around a 4 to 7 mm gap between the film and heat press top plate. One can use a metal wire to fasten the press top such that it does not close over the film and leaves a necessary gap. For best results, it is highly recommended to go by the manufacturer’s specification for powder melting. Depending upon the powder and equipment, the heating is generally done for 2 to 5 minutes with the temperature around 160 to 170 degrees Celsius.
STEP 04
Pre-pressing
The step involves pre-pressing the fabric before the transfer of the image by the film. The fabric is kept in the heat press and pressurized under heat for about 2 to 5 seconds. This is done to flatten the fabric and also ensure de-humidification of the fabric. The pre-pressing helps in the proper transfer of the image from the film onto the fabric.
STEP 05
Transfer
This is the heart of the DTF printing process. The PET film with the image and the melted powder are placed on the pre-pressed fabric in the heat press for a strong adhesion between the film and the fabric. This process is also called ‘curing’. The curing is done at a temperature range of 160 to 170 degrees Celsius for approximately 15 to 20 seconds. The film is now firmly attached to the fabric.
STEP 06
Cold Peel
The fabric and the now attached film on it must cool down to room temperature before one pulls the film off. Since the hot melt has a nature similar to amides, as it cools down, it acts as a binder that holds the colored pigment in the inks in firm adhesion with the fibers of the fabric. Once the film is cooled, it must be peeled off the fabric, leaving the required design printed in ink over the fabric.
Transfer
STEP 07
This is the heart of the DTF printing process. The PET film with the image and the melted powder are placed on the pre-pressed fabric in the heat press for a strong adhesion between the film and the fabric. This process is also called ‘curing’. The curing is done at a temperature range of 140 to 150 degrees Celsius for approximately 10 to 20 seconds. The film is now firmly attached to the fabric.
Cold Peel
STEP 08
The fabric and the now attached film on it must cool down to room temperature before one pulls the film off. Since the hot melt has a nature similar to amides, as it cools down, it acts as a binder that holds the colored pigment in the inks in firm adhesion with the fibers of the fabric. Once the film is cooled, it must be peeled off the fabric, leaving the required design printed in ink over the fabric.
Post-pressing
STEP 09
This is an optional step but is very highly recommended for best results and high-performance parameters like wash and rub fastness. In this step, the final fabric with the transferred design is pressed in the heat press for around 10 to 15 seconds.
·Speed
The same process is used whatever color or fabric type you want to print on. Therefore, production is consistent throughout and it gives you the option to create transfers in advance of needing them. For a regular customer for example, the actual production time to print the garment is quicker, if you are producing the transfers on a different day and storing them for future use.
·Hand feel
Slightly different from DTG printing. DTF has a more sheen finish to the print, yet still has a soft.
·Fabric type
One of the main reasons DTF printing has grown in popularity is that you can choose from a variety of fabrics.
By printing on the transfer film, it can then be applied to pretty much any fabric out there opening up to many garment types.
·Sustainability
How do you decide on which process your business needs? Is DTG really on the way out? I think not, and I truly believe there is space for both DTF and DTG printers in the future of garment decoration. To have a successful garment printing business, it depends on the space, budget, and overall business goals. Certainly, there are benefits in having both DTF & DTG printers. Each process requires a different type of production and order. Thus, allowing for the flexibility to choose which process is right for the job, which in turn should help the business grow in terms of profitability and quality of service to the end customer.
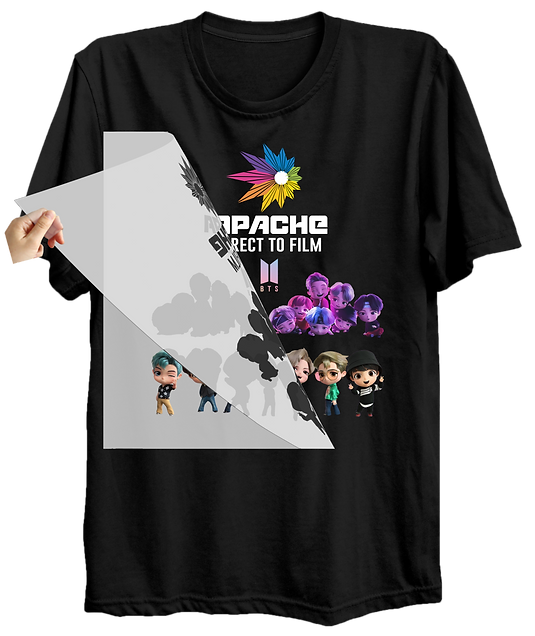

DTG PROCESS
·Speed
Because DTG prints directly onto the fabric, it is slightly quicker than DTF production at entry level, and much faster at an industrial level. In both cases you do not need to make the transfer and then apply it. When printing white or bright colored shirts, no pre-treatment is needed and as a result the production numbers would be higher with DTG than DTF. However pre-treatment is a separate and necessary process for dark shirts, and can be seen as a time consuming part of the DTG printing process, a sit is an extra step.
·Hand feel
Because you are printing directly onto the fabric, the feel of the print is softer to touch than when a transfer has been applied. No pre-treatment or white ink on bright colored garments give a perfect hand feel with DTG that cannot be replicated with DTF. At the same time, the cost per print for light DTG is highly competitive.
·Fabric type
At most levels, DTG printing is perfect for use with cotton or cotton mix garments mainly. Other materials such as polyester, nylon, or sports wear have been more of a challenge. This is where DTF really has a place in the market. However, at industrial level, DTG printing on polyester has been developed.
·Sustainability
Because the ink used in DTG is water-based and the ink is applied directly to the end garment, it is arguably the most sustainable textile printing method in the market. Less ink is wasted and no carrier material endures any damage as we see with vinyl cut and transfers of any type.
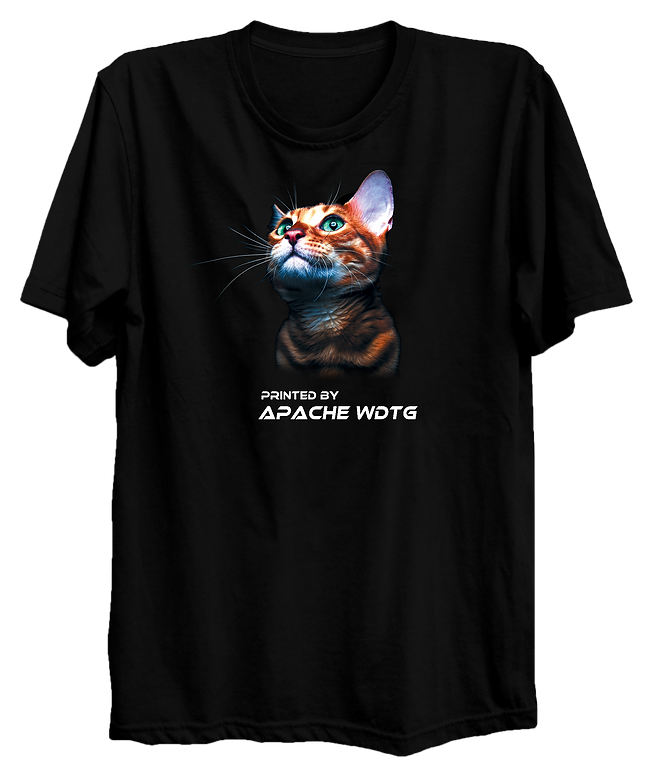

What is DTG (Direct to Garment ) printing?
Direct to Garment, or DTG printing, is a process by which a digital image is printed directly onto your apparel using cutting edge printing technology and inks. This process allows us to print any quantity order with highly detailed full color designs at an affordable price. With our expert team of direct to garment printers, any design is possible . We ensure outstanding accuracy, exceptional consistency, phenomenal print output, and affordable rates with every order.
Garments require pretreating
DTG printers require pre-treatment of clothing because the ink does not stick to clothing.
Stretchability
Images does not cracking Feels softer
Overall Cost Saving
Save your white ink up to 50%
More Durable
Works with all fabrics -
Ringspun 100% cotton, Regular (100%) cotton,
50/50 poly-cotton blends, Tri-blend (cotton, poly, rayon blend) , and more!
How to do DTG (Direct to Garment )Printing ?
01
Preparation of design
We will send the orderer a digital copy of our designer's updated work and ask for approval before printing begins.
Every order receives a professional design review from our team of graphic artists and digital printing experts.
02
Applying pretreatment to garments
Lay down the garment on a flat spray table. Make the garment even and flat. Apply the pre-treatment mix with the sprayer. Apply an adequate and even amount to where the material has an even wet sheen. Remember you only need to apply the pretreatment to the areas that will be printed on
03
Secure clothing to printer fixtures
Pretreated with a pretreatment solution, it attaches to a printer fixture designed to hold garments in place to print designs on shirts. The right positioning is crucial in order to get the desired output and not waste any textile.
Custom Apparel
From the beginning, our service was built with the customer in mind so that your ordering experience will be as easy and effortless as possible! Our online design studio makes it easy for you to customize apparel for your business, school, nonprofit organization, family reunion, and more!
Advertising and Promotions
From the beginning, our service was built with the customer in mind so that your ordering experience will be as easy and effortless as possible! Our online design studio makes it easy for you to customize apparel for your business, school, nonprofit organization, family reunion, and more!
04
Printing the image
Prepare print and image setup via Rip software or default built-in printer setup. Actual printing is taking place. With most printers, white ink comes first and colors come right after. Depending on the print mode you are using, simultaneous printing of both white and CMYK inks can take place.
Event Planning
Create decorative or promotional items for parties, weddings and more, or create custom souvenir clothing kiosks at concerts and festivals.
05
Fixation & Curing of the garment
Gently remove the printed garment, place it onto the heat press and set up the heating/pressing time. This should last about the time the ink manufacturer suggests. You can also cure the DTG-printed garments by entering them into a conveyor dryer. After that, heat is applied to dry the ink.
Optimum heatpress temperature is 160-170 oC (320-338 F).
Home Textiles
Create personalized products such as clothing, hats, backpacks, bags, leather, towels, sheets, pillows and more etc.